自喷漆掉色严重的原因通常涉及多个环节的问题,以下从材料、操作到环境因素逐一分析,并提供针对性解决方案:
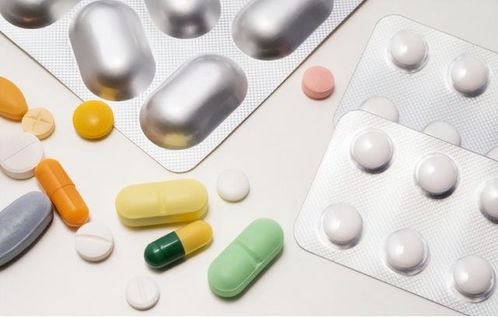
一、材料因素
1. 漆料质量问题
廉价漆料可能使用低分子量树脂(如苯丙树脂),其成膜后交联密度不足,分子链易断裂
有机颜料耐候性差(如部分偶氮颜料),在UV照射下发生光氧化反应导致褪色
溶剂体系配比不当(如快干溶剂比例过高),导致漆膜收缩应力过大产生微裂纹
2. 基材兼容性
PP/PE等非极性材料表面能低(通常<34dyn/cm),需专用底漆处理
金属表面残留防锈油(含长链烷烃化合物)形成阻隔层,影响附着力
二、工艺缺陷
1. 表面预处理不足
金属基材未进行磷化处理(磷酸锌转化膜可提升结合力3-5倍)
ABS塑料未使用异丙醇/水(7:3)混合液脱脂,残留脱模剂(硅油含量>200ppm)
打磨目数选择错误(建议400-600目形成有效锚纹结构)
2. 施工参数失当
喷涂距离<15cm导致流挂,>25cm造成干喷(漆雾未熔合)
层间间隔时间不足(溶剂型漆需15-20分钟闪干时间)
膜厚控制不当(单层>50μm易收缩开裂,<20μm遮盖力不足)
三、固化异常
1. 环境温湿度失控
温度<10℃时氨基树脂交联反应停滞(活化能>60kJ/mol)
RH>85%导致漆膜泛白(水分滞留形成微孔结构)
强制烘干时升温速率>5℃/min引发应力开裂
2. 后固化不完全
双组分漆未达到DSC曲线要求的Tg转变温度(如环氧漆需80℃/2h)
单组分漆表干后未完成深层交联(实干时间应为表干的3-5倍)
四、解决方案
1. 材料优化
选择含氟改性丙烯酸树脂体系(耐候性提升8-10倍)
搭配纳米SiO₂(添加量1-3%)增强漆膜机械强度
使用偶联剂处理基材(如KH550对金属表面接触角降低至20°以下)
2. 工艺控制
实施四阶段喷涂法:除油→喷砂(Sa2.5级)→底漆(15-20μm)→面漆(30-40μm)
采用阶梯式固化:40℃/30min→60℃/60min→室温熟化24h
膜厚检测使用Elcometer456(误差控制±3μm)
3. 品质验证
按ASTM D3359进行划格测试(达到5B等级)
QUV加速老化300h后色差ΔE<1.5(CIELab标准)
耐溶剂测试(MEK往复擦拭>100次)
通过材料科学分析与工艺参数优化,可将自喷漆的耐候寿命从常规6个月延长至3年以上。实际操作中建议建立喷涂日志,记录环境参数(温度、湿度、露点)与施工细节(枪距、走速、膜厚),便于质量追溯与工艺改进。